You hear more and more about Immersive Learning and Virtual Reality training and you are curious to exchange with those who have already stepped through? In our Stellantis immersive learning launch interview, you will discover how industry leaders have successfully implemented these cutting-edge techniques.
Discover during a professional breakfast on Friday 28 February at STATION F advice and feedback from industry leaders Alstom and Stellantis Group: why did they choose Immersive Learning to enrich their training path and how did they deploy it in France and abroad?
In anticipation of these exchanges, here is the testimony of Karen Thomas, Learning & Development Business Partner for PSA Group.
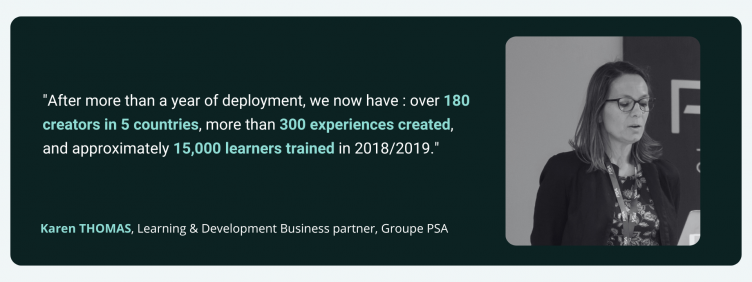
Karen Thomas is in charge of increasing the skills of employees in terms of personal development throughout the industrial and supply chain department.
Please tell us your story with Uptale and why you chose to deploy Immersive Learning ?
To sum up, we went into Immersive Learning to save time thanks to this new modality. We can still reproduce jobs in training schools, but it’s not the reality on the ground. There is no noise, no speed, no rhythm of the production line, and so on. That’s what we really wanted to portray through Immersive Learning: a “parallel reality” because they were not yet in the plant, but still in the classroom.”.
How went the adoption across the company?
Karen: “Very positive, with great verbatims from the employees. It was launched almost 2 years ago, this technology did not really exist within PSA Group, nor in other companies. It was immediately very well received by both the employees and the training/skills development department.”
Tell us about your experiences and how you are deploying it today.
Karen: “At first, we were more about presenting a typical job. Later, we developed a more transversal module, useful for all factory jobs because it deals with the warm-up procedures to be carried out before taking up a position. We have created the experiment with the physiotherapists at one of our plants in Mulhouse
Thus, while we were initially very much oriented towards the production and assembly line professions, the warm-up exercises made it possible to also reach painters, metalwork, stamping or logistics departments… This is what made the factories desire to use this technology for training. They realized that it was also possible to create Immersive expriences that were completely cross-cutting, both in terms of content and in terms of localization for distribution.
Nowadays, we count 10 sites in Europe that really use the tool/platform. Both mechanical factories (engine and gearbox manufacturing) and terminal factories (vehicle assembly), which create their own immersive training experiences.»
How are you organized internally?
Karen: “At the beginning each site was eqquiped with a VR headset so that they could at least test the warm-up experience. And it was explained that it was up to them to equip themselves afterwards, to buy the equipment they needed. And those who took ownership of the tool were able to create many experiences and train on site in Virtual Reality.
What’s important to understand is that you don’t create in a central location to redeploy, each site creates its own modules. The central unit is just here for animation, to ensure that there are no duplicates.“
Each site has a training/skills development center in which we find our logistics training pilots and training managers, usually attached to Human Resources. And each of them can help the local employees with creation.
At PSA Group there are between 40 and 100 people trained on each site with Immersive Learning. Regarding the warm-up module, it is more than 1000 learning sessions.”
People are usually comfortable using a 360 camera or creating a scenario?
Karen: “Apparently yes. However, we do have a follow-up with Corentin, Operational Pilot Industrial Efficiency at PSA Group, who has been trained directly by Uptale and who goes on site to train creators with the use of the tool and equipment.
A concrete example is that one of our sites has created 44 Virtual Reality training courses and they have made those modules availables to everyone in the group. We have the same example for quality.
What are the upcoming projects?
Karen:“What is currently planned, because this is also the advantage of Immersive Learning, is to train the night shifts.
As the teams of the training center work during the day, it was not possible to deploy training without constraints. Now with Uptale, we can easily deploy the training in night shifts, something we didn’t do before.“
Read Alstom’s interview